Not all positive displacement pumps are the same. Knowing what you need when ordering one may mean the difference between little to no maintenance with no headaches, or frequent, costly maintenance with big headaches caused by clogging or failing pumps. Paying attention to your facility’s operating needs and doing your research will not only save you from unwanted aggravation, but also pay off in spades for efficiency, cost of ownership and more.
There are a wide variety of pump styles on the market, each serving a different purpose, operating in a slightly different way and providing unique features and benefits. We previously discussed reciprocating pump designs, so now let’s examine rotary style pumps in comparison to double disc pumps.
Differences Between Rotary and Double Disc Pumps
There are many differences between a rotary style pump and a double disc style pump, including:
- Pump maintenance
- Flow variability
- Types of seals used
- Reaction to abrasive materials
- Ability to handle solids
- Ability to run dry
- Operating life between rebuilds
Overview of Rotary Pump Technology
Rotary pump technologies, like a progressive cavity or rotary lobe style, operate using rotary elements, as the name implies. These styles within the rotary design category share many of the same technology characteristics but are based on two different types of rotary technology.
- Both rotary pumps feature a close tolerance design that incorporates a rubbing action to generate flow.
- These pumps cannot run dry without damage occurring.
- They are unable to pass large solids.
- Abrasive materials, like grit and sand, will drastically increase the pump’s wear rate.
How Rotary Pumps Work
Rotary pumps are designed with a fixed stator or casing that include either a rotor or two intermeshing lobes that are moved by the rotation of the drive shaft. As these parts rotate in the casing, fluid is transported through the pump.
Both progressive cavity and rotary lobe pumps are based on a close tolerance design. These pumps require a rubbing action to generate flow. This rubbing creates what is known as ‘friction wear’ and happens even on relatively clean sludges. Because of this, the typical operating life of rotary style pump designs range from 3,000 to 5,000 hours.
Over time, the pump begins to lose efficiency. This loss of efficiency decreases the flow rate and the pump speed has to be increased to maintain the desired flow rate. As the speed increases, the pump wears faster, eventually leading to a required rebuild of the pump to reestablish its required flowrate. A rebuild is an expensive endeavor, with replacement parts running as high as 50% to 100% of the pump’s initial purchase price. The more that close tolerance pumps need to run, the more the user will see a higher cost of ownership.
Overview of PVP Double Disc Pump Technology
PVP double disc pump technology is based on a non-captive design where two discs are staged in the pump’s housing. These discs work as both the pumping element and valving element. The hydraulic interaction between the discs creates vacuum and pressure simultaneously to move fluid from suction to discharge.
Discs in PVP’s double disc pump do not experience the same type of wear and tear associated with rotary style pump designs given the reciprocating low-friction design. The pump’s trunnion sealing device is molded to flex only when the unit is in a downward stroke, extending the wear life. This trunnion seal eliminates expensive mechanical seals and the requirement for flush water systems.
How the Double Disc Pump Works
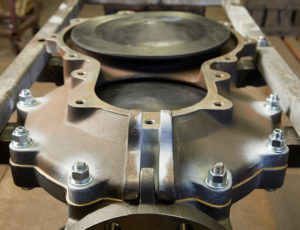
Double disc pumps have a short stroke length that produces small pulses and a relatively smooth flow. It is designed to provide positive valving on every stroke. There is no fall off in flow as the pump wears because of its reciprocating design.
A double disc pump includes a clack valve which acts as a priming and re-priming aid. It is only triggered if there is a suction lift condition or if the suction line is under a vacuum condition. Should the pump need to work during a flooded suction application, this valve does not get back to the seating surface and does not valve. It will operate without the clack valve on flooded suction applications.
The pump’s elastomeric discs also allow larger solids, rags and debris to pass through the pump, when other pumps would clog. If a piece of material is pinned beneath a disc, the flexibility of the disc material allows it to still seal around the debris and the pump continues to operate. During the next cycle, the mechanically operated discs will lift off the seat as intended, releasing the material to continue its flow through the pump. There is no ball or flapper check valve, which often clog and lead to failure in other pump designs. Depending on the pump model size, double disc pumps can handle solids up to 2 inches in diameter.
PVP’s double disc pump has a typical lifespan of 10,000 to15,000 hours and often higher because the discs are non-captive and do not experience flex fatigue failure or friction wear. These pumps can also run dry without damage thanks to the non-close tolerance design because the casing does not heat up given the low friction technology.
When You Should Consider the Use of Each Pump
Choosing the right pump for adequate fluid handling in your particular application requires you to consider many factors.
Municipal, industrial and commercial applications that process sludge, slurry, scum and other wastewater with large, submerged solids need to think about how much downtime is manageable if a pump fails before it causes facility performance and operational cost issues.
Rotary pump designs are typically lower in initial capital cost and do not produce significant pulses. Both double disc pumps and rotary pumps work similarly, but only true double disc pumps offer less clogging, less wear and less maintenance to reduce downtime and costs. Initial capital costs are only a part of the cost equation customers should be considering. The double disc pump provides a much lower lifecycle cost and is far less expensive to own and operate over the life of the pump.
Interested in learning more? Check out the whitepaper Pump Technologies for Moving High Percent Solids & Higher Viscosity Liquids